Local industries hustle to meet healthcare needs during crisis
May 7, 2020
Innovation, speed, collaboration, and follow-through.
Those seem to be the watchwords of Wayne County, Indiana industries as they respond to the coronavirus pandemic.
On Sunday, March 22, a discussion of the looming shortage of Personal Protective Equipment at Reid Health in Richmond sparked an idea. Perhaps Primex Plastics (also in Richmond) could help with face shields, suggested Brent Cotter, a Material Services Department manager. That evening, Reid Vice President Scott Rauch, who had been part of the discussion, conveyed Cotter’s idea to Dale Blunk, who works in inside sales at Primex and attends a Bible study group with Rauch.
Blunk contacted his company and by early the next morning, Reid and the Primex production and design team were working together on plans for face shields which would attach to biomedical helmets.
Doug Borgsdorf, Business Unit Director at Primex, told the Palladium-Item newspaper that a prototype was ready within 48 hours and production began within 72 hours.
On Thursday, March 26, one thousand shields were delivered to the hospital.
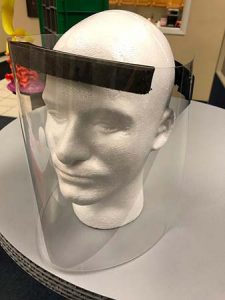
A sample of the Primex Protect face shield. (Photo supplied by Primex Plastics)
“The team at Primex truly stepped up on our behalf – and with unbelievable speed,” said Reid Health President/CEO Craig Kinyon in a news release.
And that was just the beginning.
A second kind of face shield that doesn’t attach to a helmet also was developed. Production began on the Primex Protect shield as soon as the initial shipment of helmet shields was ready.
By mid-April, Primex had shipped approximately 2 million face shields (mostly of the non-helmet variety) to 41 states and two countries, Borgsdorf said in a telephone interview.
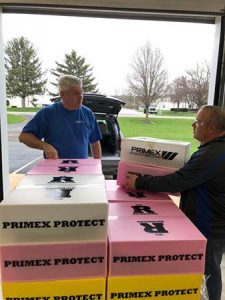
Andrew Stelle and Todd Gray load boxes of face shields for local delivery. (Photo supplied by Primex Plastics)
The demand for the shields was so vast, so immediate, and so urgent that Primex reached out to other Richmond companies for help. Borgsdorf contacted B&F Plastics and Ahaus Tool and Engineering, both of which have a strong working relationship with Primex. “Both responded within 24 hours,” he said.
Justin Scheiben at B&F Plastics said their employees began asking about getting involved in the project as soon as the news broke about what Primex was doing.
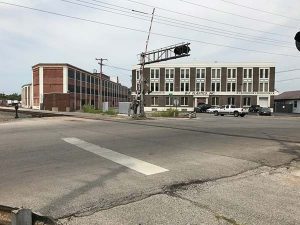
B&F Plastics, located in the Depot District of Richmond, Indiana. (Photo supplied by Louise Ronald)
“This is just great that we’re able to come together to make a product,” he said. B&F now has three shifts of four employees each daily die-cutting shields and sending them the few blocks to Primex for completion.
For Ahaus, which usually builds automated equipment to support the production processes of other companies, the shift to assembly lines for face shields has meant significant changes. “The high volume production of these medical face shields is definitely taking us out of our normal mode of business,” said Vice President and Co-owner Jeff Sheridan in a press release, “but I am proud to see our team step up to the challenge of helping our medical professionals.”
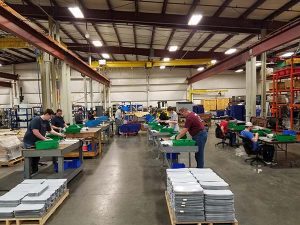
Workers at Ahaus Tool & Engineering maintain social distancing while manufacturing Primex Protect face shields. (Photo supplied by Ahaus Tool & Engineering)
“Ahaus team members have jumped into this project to help make a difference,” said President and Co-owner Kevin Ahaus in the same release. “This is a great team that cares about how they can do good things together.”
All three companies have seen employee morale soar despite long hours at what can be repetitive and less-than-exciting tasks.
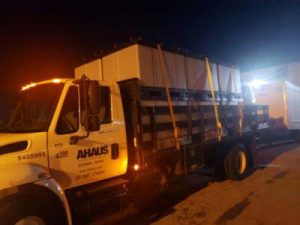
An Ahaus truck leaves the plant with a load of face shields. (Photo supplied by Ahaus Tool & Engineering)
“They’re proud to work here and be a part of helping out,” Scheiben said.
At Primex, employee interest in the project had a major impact, according to Borgsdorf.
Initially, the company thought they would be able to produce about 3,000 face shields a day over three shifts. Thanks to suggestions from the assembly line, they are more than tripling that number.
“My employees basically helped the management team come up with a way to make them faster,” Borgsdorf said.
Another Richmond company joined the project in early April.
In the beginning, Primex had a small assembly line producing boxes for shipping the face shields, but that was creating a bottleneck, said Borgsdorf.
At 8 a.m. on April 7, Primex contacted Hoosier Container, a member of Akers Packaging Service Group, about a possible order of boxes. Within an hour, Hoosier Container delivered a sample box with artwork. An hour after that, Primex submitted a purchase order for 35,000 boxes. The first 10,000 completed boxes were at Primex by 2:30 p.m. April 8 and the rest by 8 a.m. April 9.
“Their response to us was spectacular,” Borgsdorf said.
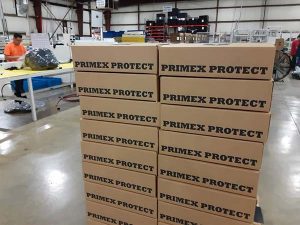
Hoosier Container stepped up to produce packaging for Primex Protect products. (Photo supplied by Primex Plastics and Hoosier Container)
This kind of collaborative effort has helped keep the cost of Primex Protect products (which now include ear protection for people who must wear masks for several hours at a time and point-of-sale transparent barriers) very competitive. The company also has a low minimum order of 100 face shields – and lowers the minimum even more for small nursing homes, medical centers, or law enforcement agencies.
B&F Plastics donated face shields to the Richmond Police Department, Reid Health Police, and the Wayne County Sheriff’s Department. An anonymous donor supplied shields to the newly organized daycare for children of essential employees at the Richmond Family YMCA. And Primex has given more than 3,500 shields to organizations and individuals suggested by employees.
Meanwhile, people are keeping their jobs. Not only that, Primex has hired nine new employees and is searching for more.
“It’s an emotional ride,” admitted Borgsdorf. But the hassles of rearranging the work floor and break schedules to accommodate social distancing have been more than offset by the thanks that keep rolling in.
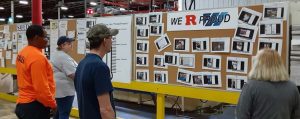
Primex employees read a bulletin board filled with thank you notes from the community. (Photo supplied by Primex Plastics)
“You have no idea the impact this has made on morale as we face this virus,” wrote a Reid nurse on the Primex Facebook page in March. The company maintains a bulletin board filled with similar comments from customers all over the community and beyond.
“We were kind of envious of the other companies like Primex that were … helping out,” Mike Owens, Vice President of Sales and Marketing at CIT (Contract Industrial Tooling) in Richmond, told the Palladium-Item.
But not for long.
CIT got its own chance to help with the pandemic starting Monday, April 6, when company founder Kim Wuertemberger was contacted by Direct Supply, a Milwaukee, Wisconsin-based seller of long-term care supplies. Would CIT be able to design and produce a “rapid-response” bed to help address the shortage of beds for COVID-19 patients?
“They didn’t even have a concept yet,” Owens said.
A concept drawing arrived the next day and CIT began working on engineering and design.
What was needed was an adjustable bed that had a surface sturdy enough to withstand medical procedures, met height specifications, and could be on casters for mobility. “They needed something functional, less expensive, and that could be turned around quickly,” said Owens.
Two days later, CIT delivered its preliminary design. A follow-up design was sent Friday and over the weekend CIT’s engineering team tweaked it further.
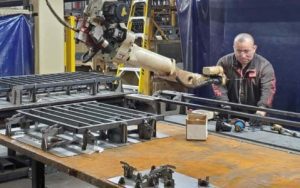
A rapid response bed is manufactured at CIT (Contract Industrial Tooling) in Richmond. (Photo supplied by CIT)
On Monday, April 13, the design was finalized. Two more days and the materials for making the beds were gathered. A prototype bed was manufactured and taken through multiple tests for reliability. By Friday, April 17, a first batch of completed beds was sent to another Richmond company, JM Hutton, for powder-coating.
“Normally this process takes eight to 12 weeks,” said Wuertemberger in a blog on CIT’s website. “We’ve done it in two weeks. To go from concept to manufacturing beds is pretty amazing.”
In fact, the first shipment of beds was headed to Milwaukee before Direct Supply had time to list the product on its website.
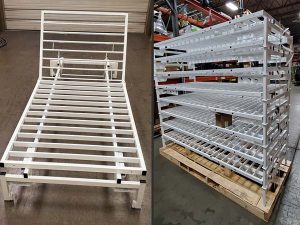
The first load of finished CIT’s rapid response beds was ready even before the seller, Direct Supply, listed the product on its website. (Photo supplied by CIT)
That kind of accelerated timeline was also evident in the development and production of two more types of Personal Protective Equipment, this time with the involvement of a doctor at Reid Health.
In March, Dr. Emily Kraft, EMS Medical Director, was following online forums with other healthcare providers dealing with the pandemic when she came across ideas for intubation sheets and intubation boxes.
Intubation – the procedure of inserting a tube so a patient can receive high flow oxygen through a ventilator – is particularly risky with COVID-19. During the procedure, the virus releases tiny droplets into the air that can infect the healthcare workers inserting the tube.
“The sheet was created based on ideas shared by other physicians across the country,” Kraft said in a press release. “It is made of high clarity, heavy-duty clear plastic sheeting that can be draped over the patient ready to be intubated ….” Kraft’s husband, Jeremy, made the first 30 sheets with items he purchased at a hardware store and Reid’s Engineering Department is making more as needed.
Intubation boxes were designed by Jared Dunlap, Director of Clinical Operations & Nursing Practice, and Engineering Director Jeff Cook’s team, based on Dr. Kraft’s idea. Cook had worked with A-Plus Signs in Richmond for many years and thought the company might be able to produce the boxes, which provide similar protection to the sheets but are preferable in some circumstances.
“We gladly accepted the project,” said Ed Thompson of A-Plus in an email. The company “turned a pencil sketch into a blueprint, then a finished product.” According to Reid’s press release, the process took less than two days.
“It feels great to be able to help our community in any way we can,” Thompson said. “I think everyone here is proud to be doing what they can for the cause.”
Employees at Tiedemann-Bevs Industries in Richmond are similarly pleased. “They are supporting a good cause and happy to be part of it,” said President and CEO Bill Jones.
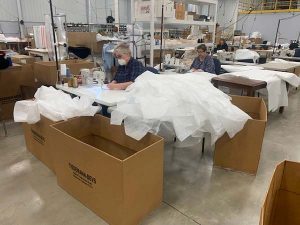
Workers at Tiedemann-Bevs protect themselves as they sew protective gowns to be distributed to Indiana healthcare facilities and other first responders. (Photo supplied by Tiedemann-Bevs)
The company, which usually makes textiles, embroideries, and snap-in panels for caskets, has added protective gowns to the list. Since mid-March, they have been producing about 1,000 gowns a week as part of an effort by the Indiana Economic Development Corporation (IEDC) to help the state meet increased demand for Personal Protective Equipment.
According to the IEDC website, more than 1.17 million items including gowns, face masks, face shields, gloves, goggles and bottles of hand sanitizer have been delivered to the Indiana State Department of Health for distribution. In all, the IEDC has secured commitments for 6.3 million pieces of Personal Protective Equipment for hospitals, first responders, long-term care facilities, and other healthcare providers treating COVID-19 patients.
Jones said he wishes Tiedemann-Bevs could do even more to help but they are so busy with their core business that there are limits on how many team members can work on the project.
Still, it feels good to be part of the solution.
The same could be said for Adam Shea, Plant Manager of Transcendia’s plastic fabrication operation in Richmond. Transcendia is a global corporation headquartered in Franklin Park, Illinois, which specializes in customizing plastic film structures.
When Shea saw an email from Sarah Mitchell, manager of Existing Business and Education at the Economic Development Corporation of Wayne County, asking if anyone knew of plastic film supplies that might be available for a Muncie plant, he thought perhaps someone in the Transcendia network might be able to help.
He sent out his own message, which was seen by Frank Reo, an Account Manager in the Healthcare division of Transcendia, who added his name to the appeal.
Mitchell’s original email was sent March 27. By April 10, Shea let her know that the Transcendia connection had born fruit. The Mursix stamping plant in Muncie would soon receive 10,000 pounds of face shield materials. (Muncie and Mursix’ headquarters in Yorktown are both are in Delaware County, Indiana, just northwest of Wayne County.)
“They’re very happy about that,” said Reo in a phone call. Shea wasn’t able to join the call, but according to Reo, Shea is proud of helping to put the Indiana company in contact with the Transcendia plant in South Carolina that was able to fill their order.
Michael Wollberg, Transcendia’s Vice President and General Manager Healthcare, praised not only Shea and Reo, but Mitchell as well.
“They were very resourceful and they all went the extra step to make sure things got done,” he said.
Innovation, speed, collaboration, and follow-through.
Borgsdorf said response to the crisis reflects well on Wayne County.
“It reminds me that this county is so much stronger than people give us credit for,” he said. “So many people here want to do great things.”